Introduction:
This art of creating life like animal statues from leather is practiced in Indore, Madhya Pradesh. Craftsmen and their families practice this craft to create miniature to life size versions of all types of animals, from horses, cows and elephants, to lions, tigers and rhinos of the jungle, to exotic creatures of the wild, like giraffes, zebras from a photographic reference..
Significance:
The leather toy-making craft is a brilliant example for showcasing the craftsmen’s talent. An accurate figurine, complete with posture details and muscular curvature, is skillfully created by the craftsmen merely using a photograph as reference. Even the patterns and textures on the skin are done with lifelike precision. The designs span from and encompass the animals in various poses and they are priced in accordance to the height of the toy. The Giraffe and elephant toys are seen to be the most popular among these. The factories usually store three bulk stocks to ensure a good rotation -“ the first batch is kept for the process of manufacturing, the second one created for foreign export markets and the third used in transportation to markets. The models are readied and stocked accordingly. The leather is stuck and is only worked upon, when orders are placed. Most of the workers involved in the craft belong to the scheduled caste or tribe and often work from home for larger export houses. Women and children are involved in the work too. Different families have specialized themselves in the various steps involved.
Usage:
The leather replicas of animals created in Indore cater to the enthusiasts of taxidermy. The animal kingdom in all shapes and sizes are made approachable using this method. They are mainly created as showpieces, furniture and souvenirs.
Introduction Process:
Leather toys are stuffed miniature replicas of animal life, created in fascinating details and variety. The craftsmen follow a skillfully devised method of working with leather to achieve a lifelike precision in appearance. The whole process involves several stages and the product is put through the hands of various artisans who are masters of their specific tasks.
Raw Materials:
Wire: Galvanized iron or mild steel is used for making the basic skeleton of any toy. The wire is generally 1mm to 4mm thick depending upon the size of the toy.
Grass / wood wool strands: It is wrapped around the wire skeleton to give mass to the body of the toy. In bigger sized models rice grass is also used for filling.
Thread: It is used to fix the grass or wood wool strands on to the skeleton. It is a regular cotton thread easily available in the market. Jute thread is used for bigger models.
Cardboard pulp: Is made by adding water and glue in the proportion of 1:20 to the cardboard powder, which is then crushed and made into a paste. Waste paper is used for packaging of items.
Glue: It is obtained from crushed tamarind seeds. Water is added to the paste. Copper Sulphate is added to the paste which acts as a preservative. Locally called ‘Layee’, it does not leave any marks on the leather. It also helps in achieving uniform paint quality.
Leather: The skin of any animal, bird or reptile. It is preserved through putrefaction, this process is called tanning. The leather used in this process is taken from goats and sheep, locally known as ‘Messi’. It comes from Chennai and Hyderabad and is the only raw material not sourced from Indore. Thickness of the leather ranges from 0.6mm to 0.8mm in skins and 1mm to 1.25mm in hides.
Eyes, teeth and soles: Eyes of the toy are available separately in the market and are made of lac material. It is available in all colors and sizes, with sizes varying from 1/4th of an inch to 2 inch depending on the size of the toy. Teeth and soles are made in plastic or polythene, created by injection molding.
Color: Synthetic water colors in powdered form, mixed with water in a proportion is decided by the craftsperson.
Polish: Wax polish, applied in the end of the process to give a shine.
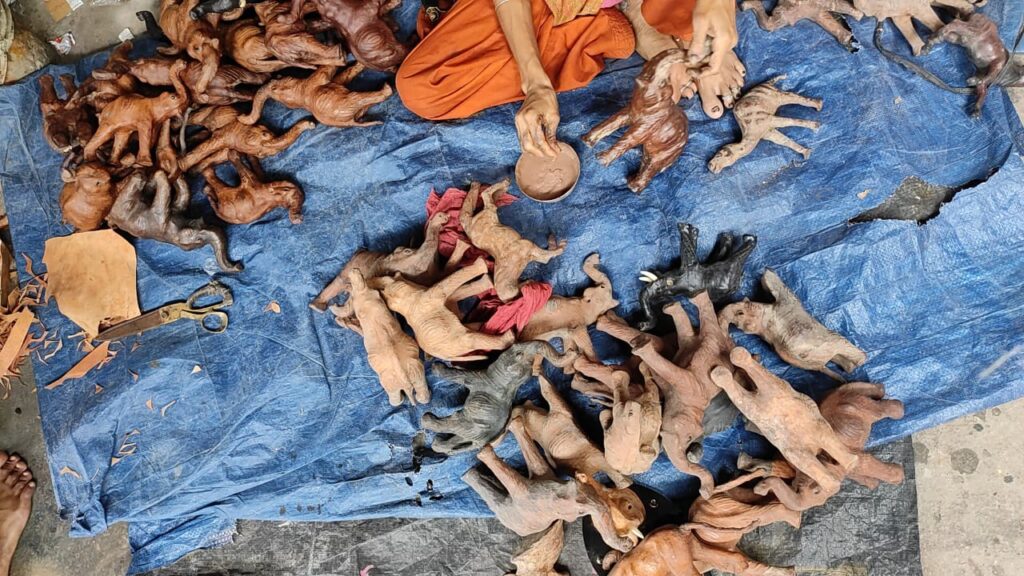
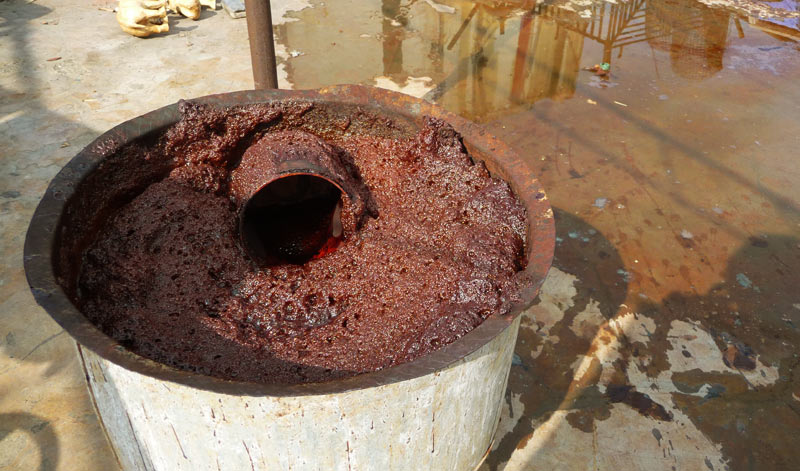
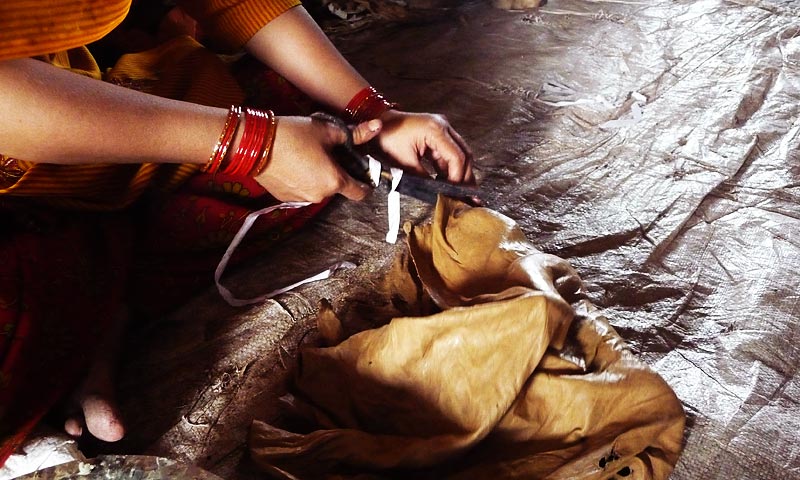
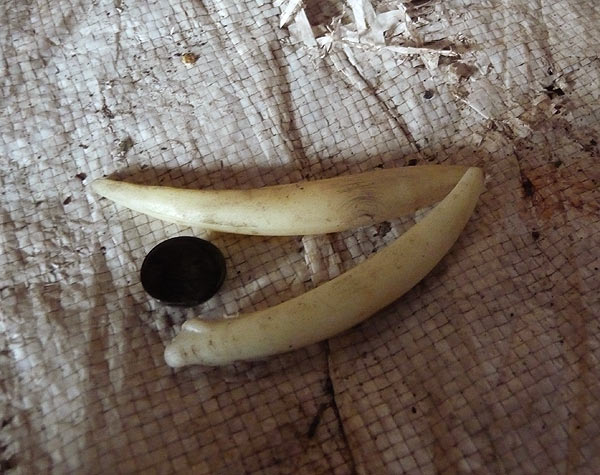
Waste:
Tools & Tech:
Hatoda (Hammer), Spoke shaver, Chaku (Knife), Poker, Awl, Fork, Paana/Taami (small tool for bending), Tocha (Fire lamp), Bubble wrapping, Blade etc.
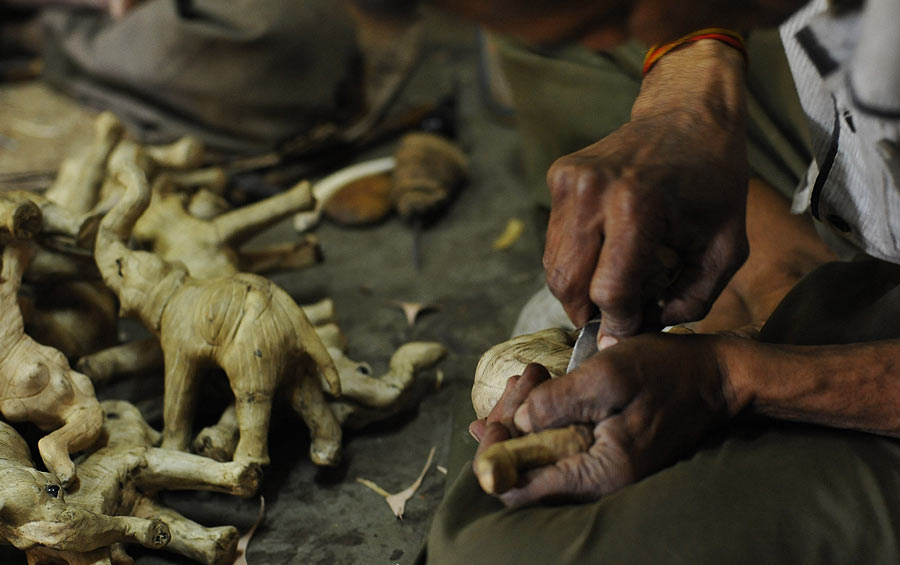
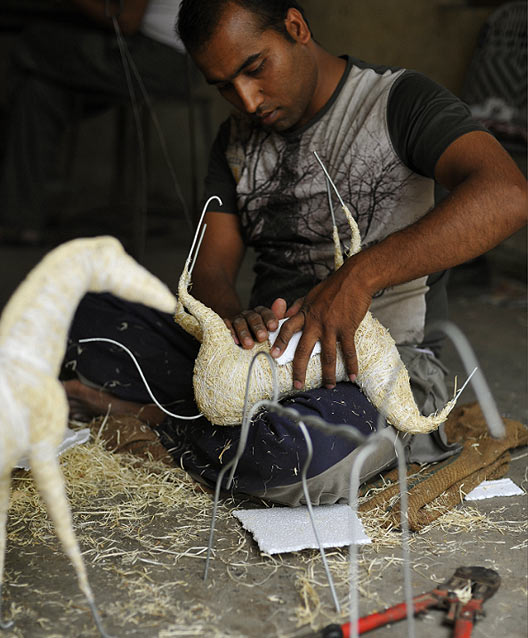
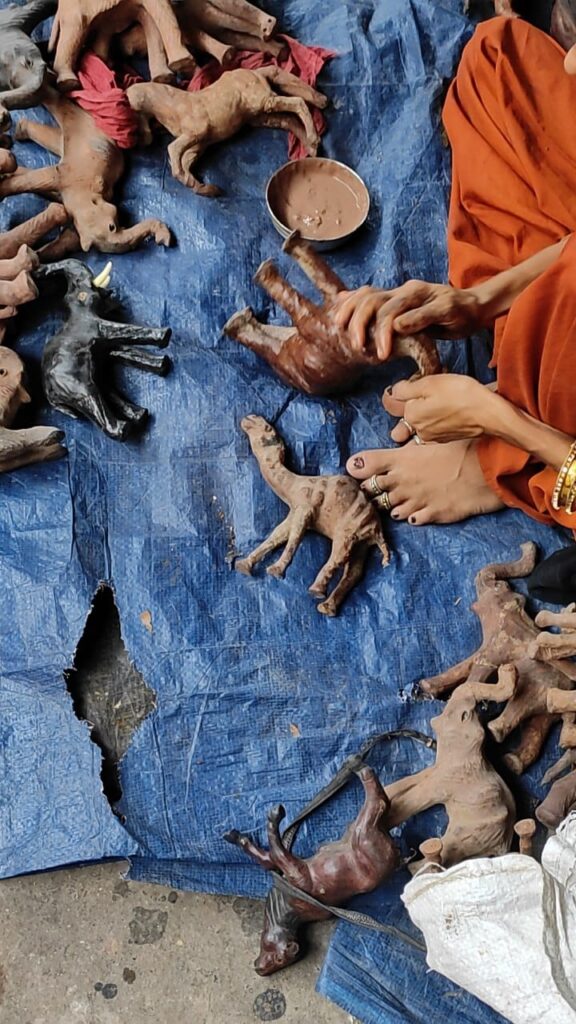
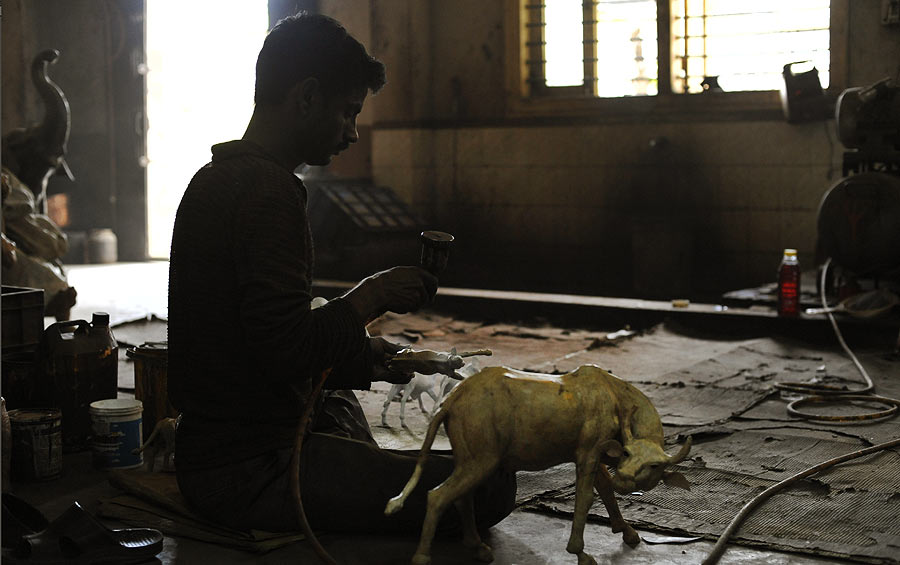
Rituals:
process:
Leather toys are stuffed miniature replicas of animal life, created in fascinating details and variety. The craftsmen follow a skillfully devised method of working with leather to achieve a lifelike precision in appearance. The whole process involves several stages and the product is put through the hands of various artisans who are masters of their specific tasks.
Wire-frame
When the artisan sets out to make the toy, the form is clear in his mind. He begins the process by taking metal wires and makes a wireframe for the toy. When the wireframe is completed, one can already see the kind of animal which the wireframe will mature into. In next stage the artisan takes grass or hay and ties it around the wireframe with a thread. When this stage is concluded, the toy has already gained the necessary form of the visualized animal and the hay helps in keeping the weight of the toy to minimum.
Molding
A pulp is made with waste cardboard or sawdust and tamarind flour. It is applied over the frame to smoothen out the form. The artisans involved in molding process are experts in depicting salient features of anatomy.
If a large number of identical pieces have to be made, a fiber mold is designed. The pulp is filled into the same and shaped according to the mold. Once the pulp attains a rigid shape, the artisan adds final muscular finishes with his fingers or with other basic tools such as discarded comb handles and forks. Sometimes, the artisans add further finishes by attaching clay and fine pulp to the already realized form.
Sticking the leather
Rags are wrapped around the lower legs of the frame and covered with pulp to get the desired shape. Tamarind powder is boiled and made into glue, which is used to apply over the form. The leather is then stuck onto the form with the help of this glue. It requires great skill to put leather accurately over the animal form, the artisan makes sure that there are no wrinkles and there is no air trapped between leather and the pulp body. Different leather pieces are smoothened from the edges to have low thickness so that the overlapping of leather pieces does not result into irregularities. The artisan tries to place the joint in leather pieces beneath the animal body.
Finishing
After the leather is stuck, the finishing is done by rubbing a smooth stone over the wet leather. A blunt knife is used to put features on the streamlined body of the animals. The piece is kept to dry for almost 15 days. The drying out of leather is very important because if any moisture remains, it will cause the leather to expand later and warp leading to a decrease in quality. The artisans then finally attach eyes, teeth to the object. These are then bubble wrapped and packed in cartons.
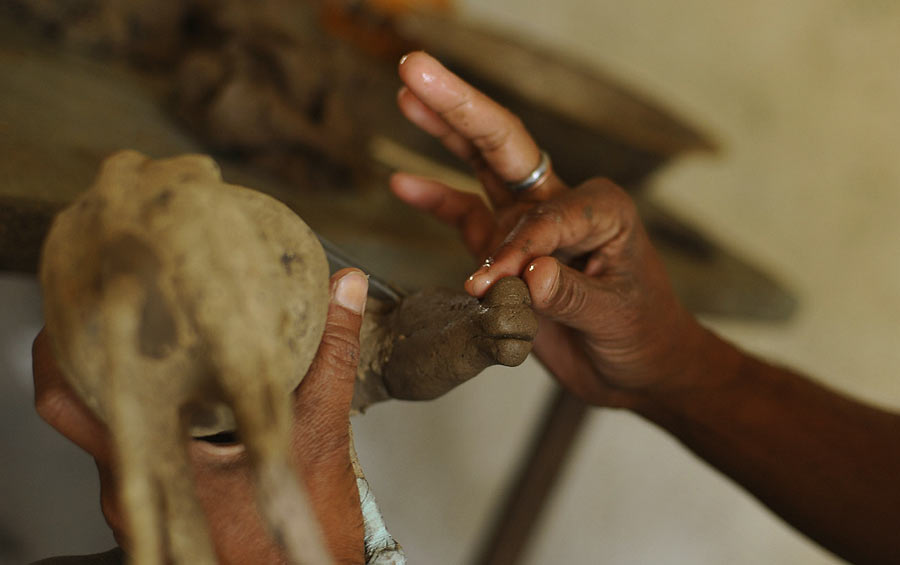

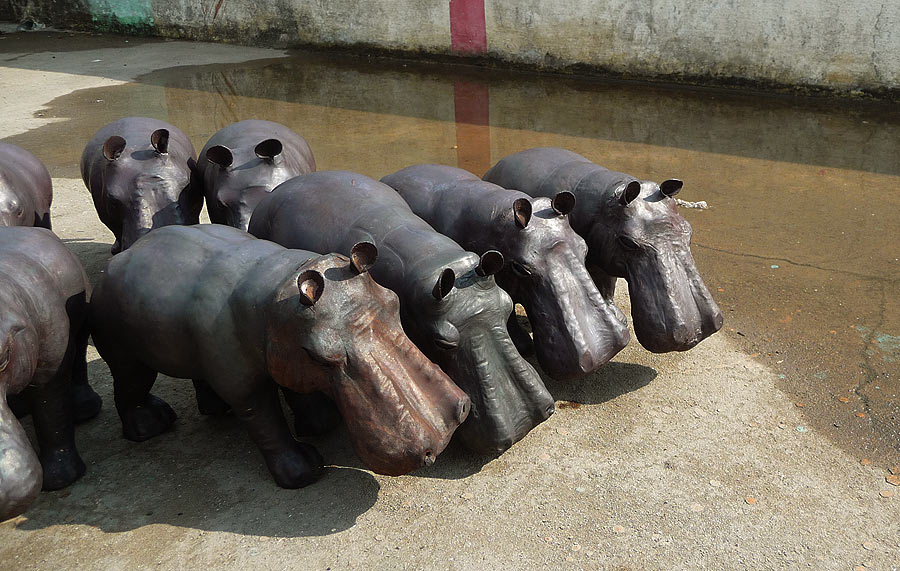
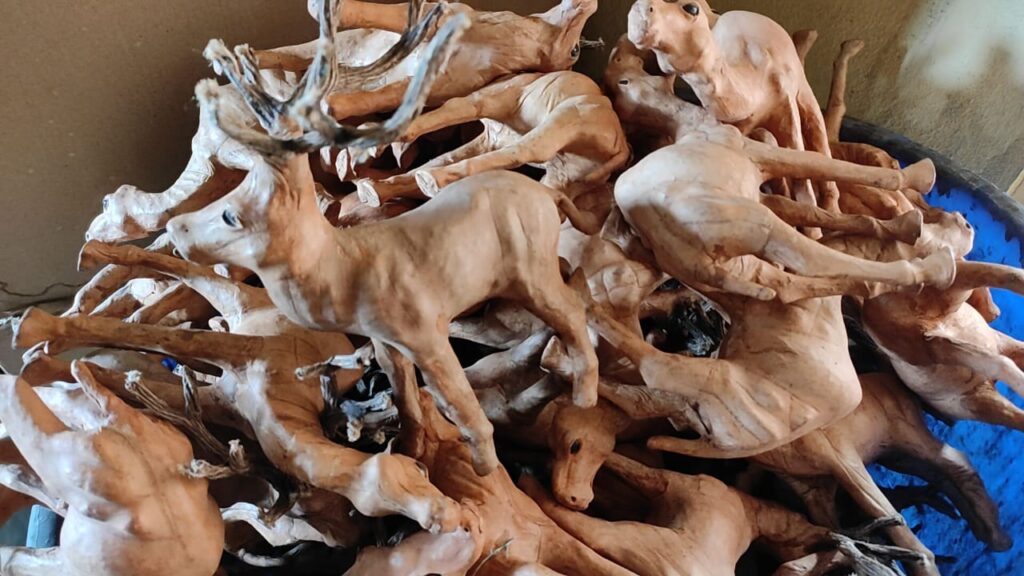
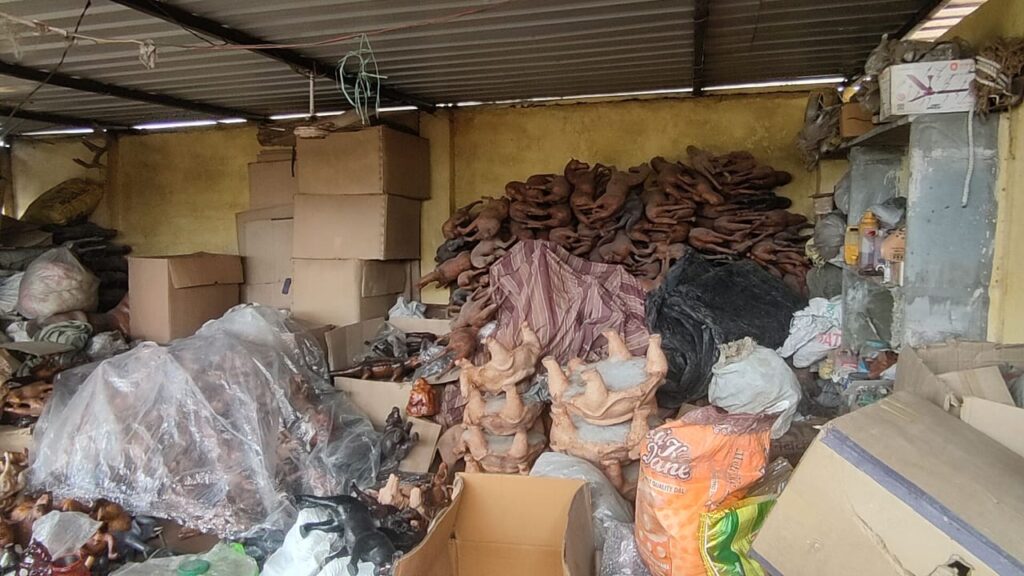
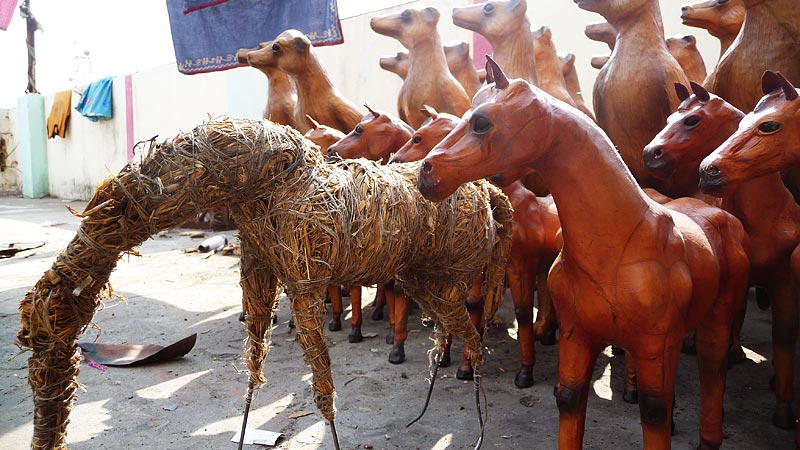
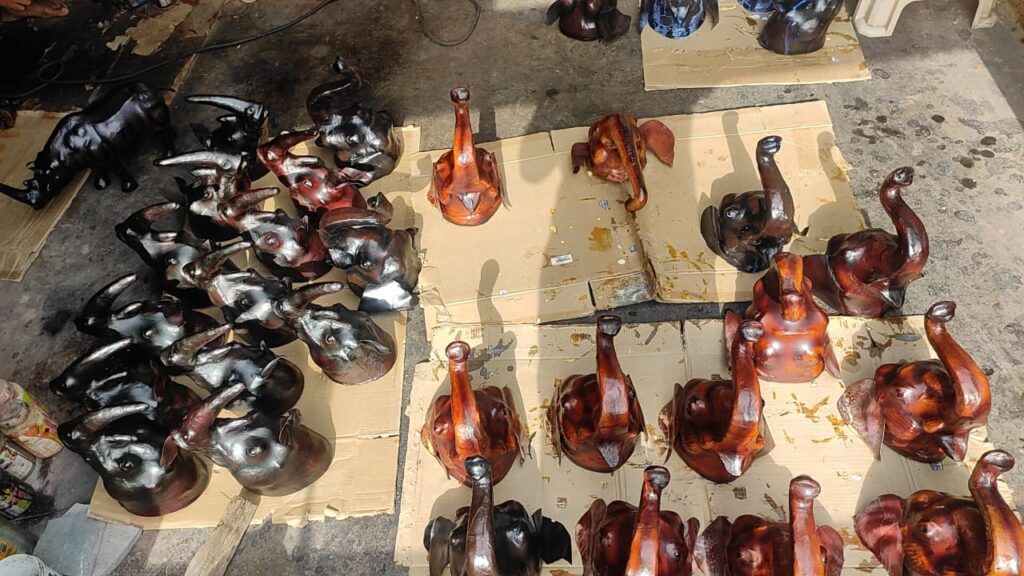
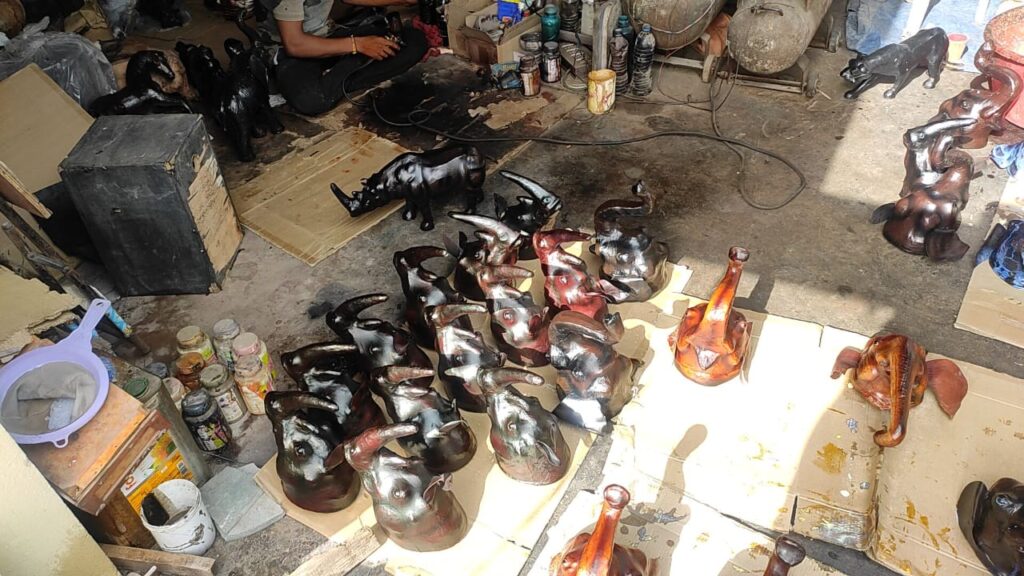